Integration der Nutzung von Abfallressourcen in die globale PHA C2G-Plattform (Cradle-to-Grave)
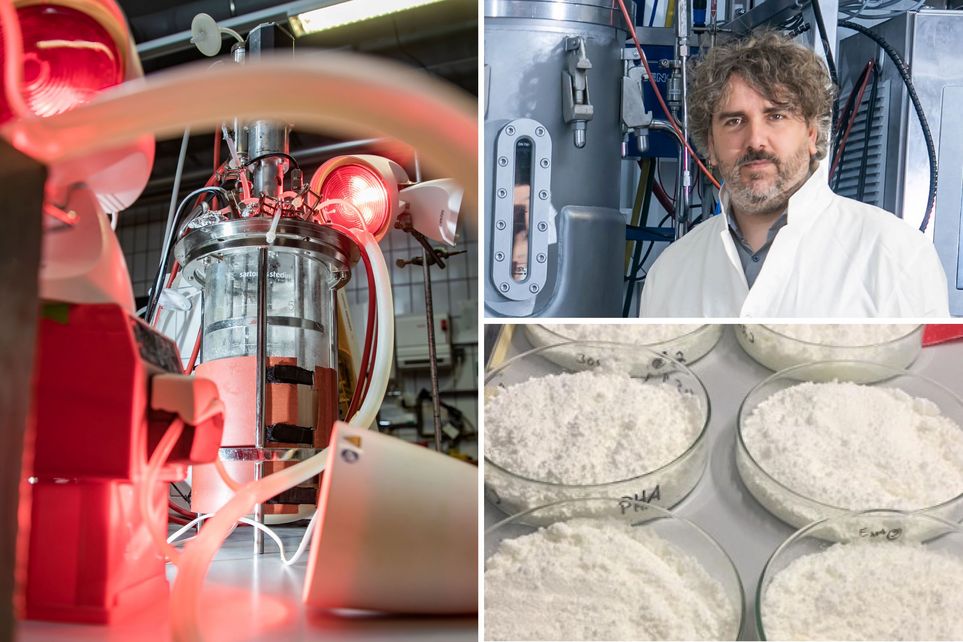
Im Jahr 2023 wurden weltweit über 400 Millionen Tonnen Kunststoff produziert – der Großteil auf Basis fossiler Rohstoffe. Nur 9,3 Prozent bestanden aus recyceltem Material, lediglich 0,7 Prozent waren biobasiert (Quelle). Doch auch biobasierte Kunststoffe sind nicht automatisch umweltfreundlich: Rund die Hälfte der biobasierten Kunststoffe ist überhaupt nicht biologisch abbaubar. Viele der übrigen lassen sich nur unter speziellen Bedingungen, etwa in industriellen Kompostieranlagen, zersetzen. In der Natur bleiben sie hingegen oft als Müll in Meeren, Flüssen oder Böden zurück. Die wenigen Kunststoffe, die tatsächlich vollständig abbaubar sind, stammen meist aus Lebensmitteln wie Mais oder Raps – was wiederum Flächenkonkurrenz zur Nahrungsmittelproduktion schafft.
Prof. Dr.-Ing. Sebastian Riedel von der Berliner Hochschule für Technik (BHT) und Prof. Dr. Jaewook Myung vom Korean Advanced Institute of Science and Technology (KAIST) entwickeln gemeinsam ein Verfahren, das biologisch abbaubare Kunststoffe aus Abfallstoffen wie altem Speiseöl oder Frittierfett produziert – ganz ohne neue Flächen zu beanspruchen. Gefördert wird das Vorhaben von der Deutschen Forschungsgemeinschaft (Projektnummer 551314136).
Mikroben machen’s möglich
Herzstück des Verfahrens ist das Bakterium Cupriavidus necator. Es kann verschiedenste Kohlenstoffquellen – darunter auch Küchenabfälle – aufnehmen und in seinem Zellinneren in Polyhydroxyalkanoate (PHA) umwandeln. Diese biologisch abbaubaren Polyester besitzen thermoplastische Eigenschaften und können konventionelle Kunststoffe ersetzen.
Doch der natürliche Bakterienstamm produziert PHA mit kurzen Seitenketten. Diese sind spröde und für viele Anwendungen ungeeignet. Deshalb setzen die Forschenden auf einen gentechnisch optimierten Stamm, der auch Polymere mit mittelkettigen Seitenketten herstellt. Diese sind deutlich flexibler – ideal für Produkte wie Folien, Tüten, Beschichtungen oder Spritzgussteile. Und das Beste: Sie zerfallen vollständig in der Umwelt – auch im Meerwasser – ganz ohne schädliches Mikroplastik (zum Paper).
Maßgeschneiderter Kunststoff aus dem Reaktor
Damit die Bakterien optimale Bedingungen vorfinden, werden sie in sogenannten Bioreaktoren kultiviert. Dort halten die Forschenden Temperatur, pH-Wert und Sauerstoffzufuhr konstant. Gefüttert wird mit Abfallölen und gezielt ergänzten Stoffen, sogenannten Cofeeds, die die Eigenschaften der Polymere beeinflussen. Ein Beispiel: Wird dem Speiseöl Propionsäure beigemischt, entsteht ein Polymer namens P(HB-co-HV-co-HHx). Je nach Verhältnis der Monomere verändert sich die Schmelztemperatur, Härte und Verarbeitbarkeit. Mit einem höheren HHx-Anteil wird das Material weicher, biegsamer – und damit industriell vielseitiger einsetzbar.
PHA dient dem Bakterium als Energiespeicher und wird vor allem dann gebildet, wenn die Zelle unter Stress gerät. Wird beispielsweise gezielt Stickstoff oder Phosphat entzogen, stoppt das Zellwachstum, während das vorhandene Öl weiterhin in Kunststoff umgewandelt wird. Ziel ist es, vor Eintritt dieser Nährstofflimitierung eine möglichst hohe Bakterienzahl zu erreichen. Denn je mehr Zellen, desto mehr PHA. Aktuell dauert dieser Prozess 60 bis 70 Stunden. Durch eine verbesserte Vorkultivierung wollen die Forschenden die Zeit im Hauptreaktor auf 48 Stunden verkürzen. Ein weiterer Knackpunkt: Schaumbildung im Reaktor. Sie kann zum Überlaufen oder zu Verstopfungen führen. Hier helfen mechanische Schaumbrecher und eine präzise Dosierung der Öle.
Von der Zelle zum Plastik
Nach der Kultivierung wird die Bakterienmasse mithilfe eines Tellerseparators von der Flüssigkeit getrennt. Anschließend wird das PHA durch mechanische, biologische oder chemische Verfahren aus dem Zellinneren freigesetzt. Zur Analyse wird ein Gaschromatograph mit Flammenionisationsdetektor (GC-FID) eingesetzt. Er bestimmt, welche Monomere im PHA enthalten sind – deren Zusammensetzung hat direkten Einfluss auf die Eigenschaften des Kunststoffs. Im nächsten Schritt geht das Material nach Südkorea, wo Prof. Myung die biologische Abbaubarkeit prüft. Zusätzlich testet er, ob sich auch regionale Agrarabfälle als Rohstoff eignen. Dabei greift er auf die in Berlin optimierten Prozesse zurück.
Langfristig wollen Riedel und Myung mit ihrer Forschung einen Beitrag zur nachhaltigen Kunststoffproduktion leisten. Ziel ist es, die Prozesse ressourcenschonender zu gestalten und die Abhängigkeit von fossilen Rohstoffen zu verringern. Ihre Arbeit könnte den Weg ebnen für den breiten Einsatz biologisch abbaubarer Materialien in der Industrie – aus Abfall, für die Umwelt.